A menudo, las únicas pruebas y acciones que se efectúan en un sistema hidráulico implican cambiar los filtros, tomar muestras del aceite y verificar el nivel de aceite. Mientras el sistema esté en funcionamiento, prevalecerá con frecuencia la mentalidad de «si no está dañado, no lo arregle». Sin embargo, en cualquier sistema en su planta, debe realizar entre 15 a 20 pruebas regulares de confiabilidad mientras el sistema está funcionando. También hay varias verificaciones y procedimientos que deben completarse durante las paradas o los días de inactividad. Las siguientes pruebas de mantenimiento preventivo y confiabilidad pueden ayudar a mejorar la eficiencia y el funcionamiento de sus sistemas y máquinas hidráulicas.
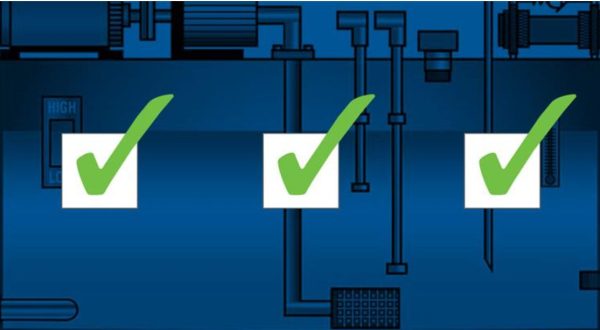
Figura 1. Ejemplo de un depósito de aceite en un sistema hidráulico.
1 = Termostato del calentador 4 = Respirador
2 = Cedazo de succión 5 = Interruptor de alta temperatura
3 = Ajustes 6 = Intercambiador de calor
Compruebe el depósito de aceite
Un buen momento para revisar el depósito de aceite es cuando su planta o sistema está fuera de operación. Los mecánicos y los electricistas de mantenimiento generalmente se ríen cuando les digo que el depósito debe limpiarse al menos una vez al año. Un mecánico de una gran planta de productos de madera me dijo que el depósito de un sistema no se había limpiado desde que comenzó a funcionar la fábrica hacía 17 años.
Aparte del almacenamiento de aceite, los dos propósitos principales del depósito de aceite son disipar el calor y permitir que los contaminantes (agua, aire, partículas sólidas) se separen del aceite. Si el depósito no se limpia, no solo disminuirá su capacidad de disipar el calor, sino que también actuará como un acumulador de calor. Las temperaturas pueden elevarse fácilmente por encima del nivel máximo recomendado de 60 ºC (140 ºF). A partir de esta temperatura, el aceite comenzará a degradarse con mayor rapidez, lo que provocará la formación de lodo y barniz en el sistema. Si los contaminantes no se eliminan del depósito, se introducirán en la bomba, lo que provocará un fallo prematuro de los componentes del sistema.
Muchos depósitos de aceite contienen un filtro o cedazo en la succión para evitar que entren partículas grandes a la bomba. La mayoría de los cedazos en la succión tienen una clasificación de 74 micrones, mientras que las tolerancias dentro de las bombas y las válvulas suelen ser de 3 a 8 micrones.
Utilice siempre una toalla que no suelte pelusa para limpiar un depósito de aceite. Si se emplea un solvente, asegúrese de que sea recomendado para sistemas hidráulicos. Incluso pequeñas cantidades del solvente incorrecto pueden dañar ciertos aditivos y los sellos de elastómeros.
Lavado y limpieza del sistema
Al drenar el aceite del depósito para efectuar la limpieza, debe filtrarse y trasnferirse a un tanque de almacenamiento con una unidad de lavado y filtrado que tenga la capacidad de eliminar contaminantes sólidos y agua. Utilice un filtro de calidad y alta eficiencia de captura (tasa beta de filtración, de acuerdo con ISO 16889) que coincida con el nivel de limpieza objetivo del sistema. A menos que el aceite esté severamente degradado, no es necesario ni deseable cambiarlo.
Después de limpiar el depósito, introduzca el aceite de regreso al depósito del sistema hidráulico haciéndolo pasar a través de los filtros o utilizando un carro de filtración. Luego, se debe hacer circular por todo el sistema para limpiar las tuberías, las válvulas y los actuadores.
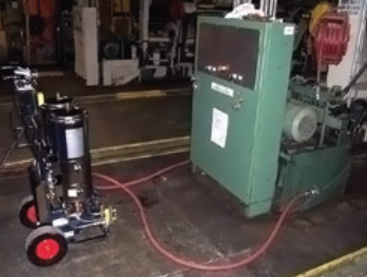
Figura 2. Se puede usar una unidad de filtración para eliminar
los contaminantes sólidos y el agua del aceite.
El lavado del sistema se realiza conectando las tuberías de entrada y salida de los cilindros y motores. Si es posible, accione eléctrica o manualmente las válvulas direccionales para permitir que el fluido circule a través de las tuberías. Si esto no es posible, ponga en derivación las válvulas direccionales conectando las tuberías de presión y del depósito a las tuberías de salida de los actuadores. Utilice la bomba existente en el sistema para recircular el aceite a través de las tuberías. Conecte una unidad de lavado de alta velocidad para que recircule el aceite en el depósito a través de los filtros durante el proceso de lavado. Permita que el sistema funcione durante el mayor tiempo posible.
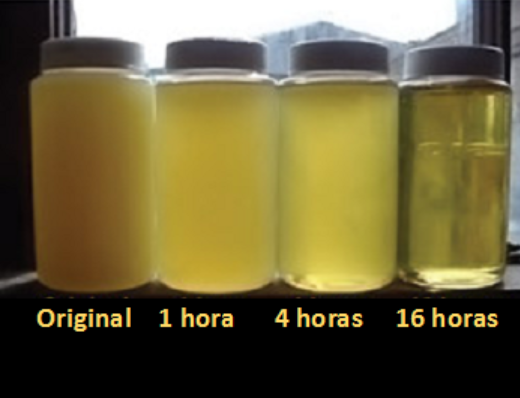
Figura 3. Se muestra la pureza del aceite para un sistema antes de ser lavado (izquierda)
y después de una, cuatro y dieciseis horas. Este sistema en particular tenía un alto contenido de agua antes del lavado.
Verifique la configuración del calentador del depósito
Muchas veces, el calentador se desconecta durante el verano o se puede haber omitido cuando el sistema se diseñó inicialmente. Verifique el termostato del calentador en el depósito para confirmar que se encenderá a una temperatura mínima de 21 ºC (70 ºF). Si la bomba está montada en la parte superior del depósito y la temperatura del aceite desciende por debajo de aproximadamente 16 ºC (60 ºF), entonces puede presentarse cierto grado de cavitación en la bomba.
Ajuste los sensores de nivel de aceite
La mayoría de los depósitos utilizan dos configuraciones del sensor: advertencia y apagado. El problema es que la diferencia entre estos dos niveles puede ser de varios cientos de litros de aceite. Al eliminar el interruptor de advertencia y configurar el de apagado a un nivel más alto, la pérdida de aceite será mínima si se rompe una manguera.
Compruebe la condición del respirador
El respirador suele ser el componente más descuidado en el depósito. Verifique que el filtro respirador de aire tenga una eficiencia de captura que coincida con la limpieza objetivo del fluido. Esta es la primera línea de defensa para evitar que los contaminantes entren al depósito. Dependiendo de su ubicación y el grado de contaminación en el entorno, es posible que el respirador deba cambiarse un par de veces al año. Muchos respiradores tienen un indicador mecánico que proporcionará una indicación visual cuando el elemento está obstruido. Otras opciones para evitar el ingreso de contaminantes son presurizar el reservorio con una cámara de expansión o usar un tipo de respirador que elimine también la humedad. Recuerde que el dinero gastado mejorando el respirador de su depósito nunca será un desperdicio.
Ajuste el interruptor de alta temperatura
El aceite mineral comenzará a degradarse a partir de los 60 ºC (140 ºF), pero muchos sistemas no apagarán la unidad hasta que la temperatura del aceite alcance los 70 ºC (aprox. 160 ºF). Los sistemas hidráulicos están diseñados para funcionar a menos de 60 ºC. Por cada 10 ºC (18 ºF) que incremente la temperatura del aceite por encima de 60 ºC (140 ºF), la vida del aceite se reducirá a la mitad. Si la temperatura del aceite sube por encima de ese nivel, entonces existe un problema en el sistema. Esto podría ser causado por un mal funcionamiento del enfriador o porque la bomba está derivando aceite excesivamente. Fije el interruptor de alta temperatura a 60 ºC para el apagado de la bomba, evitando la degradación del aceite.
Lavado y limpieza del intercambiador de calor
En un intercambiador de calor con agua (del tipo carcasa y tubos), el aceite fluye por afuera de los tubos y el agua fluye a través de los tubos en la dirección opuesta. El calor se transfiere del aceite al agua. Para lograr una transferencia de calor más eficiente, el flujo de agua debe ser el 25 por ciento del flujo de aceite. El flujo de agua se puede controlar mediante válvulas manuales, una válvula moduladora de agua o una válvula solenoide eléctrica. Puede circular aceite de lavado caliente o un destilado ligero a través de los tubos o del lado de la carcasa, lo que permite eliminar de manera efectiva el lodo o depósitos blandos similares. Los depósitos de sal (sarro) se pueden limpiar haciendo circular agua caliente y fresca. Se puede usar una solución alcalina suave como Oakite o una solución de hidróxido de sodio o ácido nítrico al 1.5 por ciento. Los tubos deben lavarse en la dirección opuesta a la que normalmente fluye el aceite.
Si se emplea un enfriador de aire, verifique que el ventilador del enfriador se encienda aproximadamente a 50 ºC (120 ºF) y se apague aproximadamente a 40 ºC (105 ºF). Mantenga limpias las aletas del radiador, de tal forma que pueda verse la luz a través de ellas. Si es necesario, deben utilizarse peines para enderezar las aletas de la unidad. Al limpiar las aletas con aire comprimido, se debe tener cuidado de no dañarlas.
Pruebas a la bomba
En bombas de volumen variable, verifique el flujo que sale de la línea de drenaje de la carcasa, haciendo llegar la tubería a un contenedor y midiendo el tiempo. Esta prueba debe realizarse con la presión de salida al nivel máximo. No se recomienda sostener con la mano la tubería durante esta prueba. Asegure la tubería al contenedor antes de encender la bomba. El flujo normal de la carcasa es del 1 al 5 por ciento del volumen máximo de la bomba. Las bombas de paletas generalmente pasan en derivación más flujo que las bombas de pistón. Si de la tubería de drenaje de la bomba sale el 10 por ciento del volumen máximo, debe cambiarse la bomba. Un método excelente para monitorear el flujo de drenaje de la bomba durante la operación es instalar permanentemente un medidor de flujo en la línea de drenaje de la bomba.
Las bombas de desplazamiento fijo se pueden probar verificando el flujo a través de la válvula de alivio. Encienda la bomba y registre el flujo que sale de la tubería que va al depósito por la válvula de alivio durante un minuto. A continuación, reduzca la configuración de la válvula de alivio a su ajuste mínimo. Debe haber una diferencia de menos del 10 por ciento entre las tasas de flujo de las dos pruebas. Si una bomba está muy desgastada, el flujo será considerablemente menor a la presión más alta.
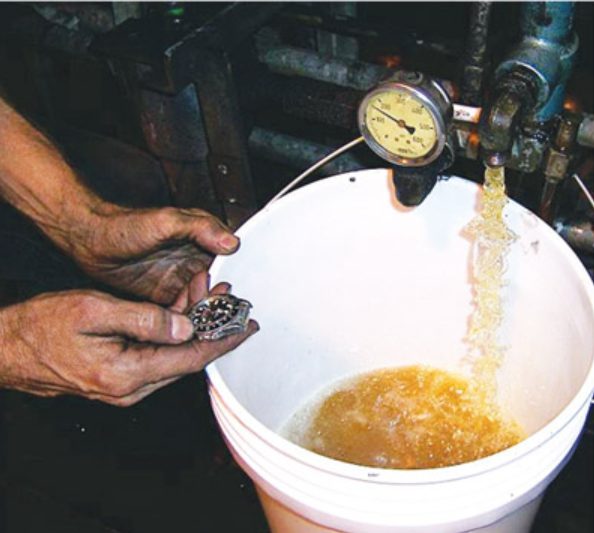
Figura 4. Pruebe una bomba de desplazamiento fijo encendiendo la bomba y
registrando el flujo que sale de la tubería del depósito por la válvula de alivio durante un minuto.
Pruebas al acumulador
Un acumulador debe precargarse con nitrógeno seco entre la mitad hasta dos tercios del ajuste del compensador de la bomba. Cuando se apaga el sistema hidráulico, se puede utilizar una dispositivo de carga con un manómetro para verificar el nivel de precarga.
Para confirmar que un acumulador está funcionando correctamente, verifique el lado de la carcasa con una pistola de temperatura o una cámara infrarroja. La mitad inferior debe estar más caliente que la mitad superior. Si solo se localiza calor en la parte inferior, el acumulador puede estar sobrecargado. Si no hay calor, la vejiga puede haberse roto, los sellos del pistón pueden estar dañados, la precarga puede estar por encima del ajuste del compensador o puede haberse fugado todo el nitrógeno. Si el calor se siente completamente en la parte superior, la carga es insuficiente.
Otra comprobación que se puede hacer es observar el medidor de presión del sistema mientras está funcionando. Normalmente, la presión no debe caer más de 100-500 libras por pulgada cuadrada (psi, por sus siglas en inglés) cuando el acumulador está debidamente precargado.
Si se utilizan acumuladores de pistón, el dispositivo de carga debe instalarse cuando el sistema está abajo y se ha purgado el aceite en la parte superior del pistón. Con la bomba encendida y la válvula de purga abierta, debe haber poco o ningún flujo de la válvula de purga. Se debe tener cuidado de que todo el personal esté lejos de la válvula de purga antes de encender la bomba. Si hay flujo continuo, los sellos del pistón o el cilindro pueden estar dañados. Si no existe flujo, recargue el acumulador al nivel adecuado de nitrógeno seco.
Comprobación de mangueras
Verifique que todas las mangueras del sistema tengan la longitud y el desgaste en rango adecuado. Las mangueras rara vez revientan debido a que se excede la presión de trabajo nominal, sino más bien debido a un roce o frotamiento deficiente contra una viga, otra manguera, el piso, etc. Existen diversas fundas y soportes para mangueras de distintos fabricantes en caso de que no se pueda evitar el roce. Las mangueras generalmente no deben exceder 1.20 metros (4 pies) de longitud, a menos que se muevan con la máquina.
Además, examine la tubería del sistema para verificar que se haya instalado una manguera antes de conectarla a un banco de válvulas o un cilindro. La manguera absorberá el choque hidráulico generado cuando el aceite salga rápidamente. Una excepción a esta regla es que se debe usar tubería rígida cuando se conecta a una carga vertical o suspendida. Se pueden emplear válvulas check operadas por piloto y válvulas de contrapeso para mantener la carga en la posición elevada.
Inspección de abrazaderas
Inspeccione las abrazaderas del sistema para confirmar que sean del tipo correcto para las líneas hidráulicas. Las abrazaderas en U con tornillos (tipo viga) y para tubo conduit no son aceptables, ya que no absorberán el choque generado en la tubería. Las abrazaderas deben tener una separación de aproximadamente 1.50 metros (5 pies) e instalarse a 15 centímetros (6 pulgadas) del punto de terminación de la tubería.
Pruebas en válvulas
En cualquier sistema, una o más válvulas se cerrarán mientras el sistema esté funcionando. Entre ellas están las válvulas de alivio usadas con bombas compensadoras de presión, válvulas de purga de aire y válvulas de descarga del acumulador. Las tuberías de estas válvulas hacia el depósito deben verificarse regularmente con una pistola de temperatura o una cámara infrarroja para verificar que las válvulas estén cerradas y que no se pierda aceite hacia el depósito.
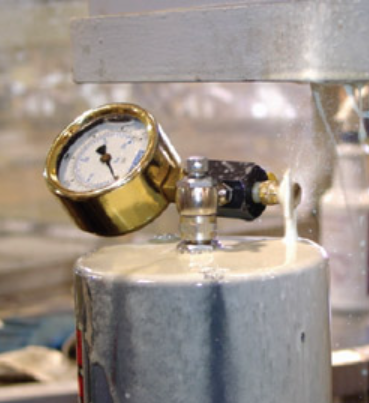
Figura 5. El flujo continuo de una válvula de purga puede indicar sellos de pistón desgastados.
Debe desarrollarse un programa de confiabilidad y mantenimiento preventivo para cada uno de los sistemas hidráulicos en su planta. Al realizar estas pruebas, sus sistemas funcionarán de manera más segura y con la máxima eficiencia, a la vez que reducirán el tiempo muerto no programado.
Noria Corporation. Traducido por Roberto Trujillo Corona, Noria Latín América.